Grinding and Testing of Telescope Mirrors – Part 1
Tech info | July 10, 2022
A brief introduction
Ever since the world began, man's gaze has always been directed upwards, towards the sky and the stars, towards the divine worlds. This is evidenced by all the sacred books of humanity and by many ancient cult complexes and megalithic structures spread everywhere on our planet. With the development of his knowledge of the world, man has created many advanced tools to observe and study the celestial spheres. The invention of the telescope in the 16th century by Dutch optical masters and its use in 1609 by the Italian mathematician and astronomer Galileo Galilei (1564-1642) to observe celestial bodies marks a new epoch in science and human civilization. An interesting fact is that Galileo died in 1642, the same year that another great scientist - Sir Isaac Newton, was born. So, the baton has been successfully passed forward. In addition to his fundamental scientific discoveries, Newton also created the first mirror telescope. To this day, the most used optical configuration for amateur telescopes bears his name. He has left many ideas and drawings of mechanical tools and machines for grinding lenses and small optical parts. So, Sir Isaac deserves to be considered the founder of modern optical manufacturing and telescope building.
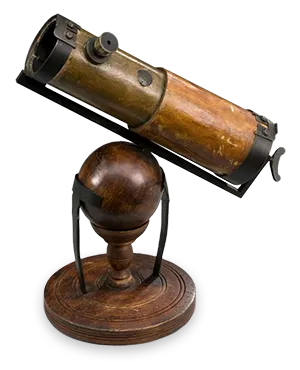
In the following centuries, science continues to evolve in both theoretical and practical aspects. Optical instrument making is also improving, already placed on a scientific and technological basis. In the middle of the 19th century, the German mathematician Philipp Seidel expanded the aberration function in a power series and thus opened the way for the analytical construction of optical systems with corrected aberrations. The wave theory of light was created too. In 1858, the French physicist Leon Foucault invented the first method for testing optical systems, known as the knife-edge test, thus allowing the opticians to see
the quality of the optical surfaces they manufacture. Photography was developed, which brings the need for more precise lenses and cameras. With the progress of chemistry, glassmaking was also improved, and so was the production of the new types of glass used in optical parts. It should be mentioned the theoretical studies and experiments of Young, Fresnel, Arago, Gauss, Herschel, Abbe, J.C. Maxwell, Airy, Fizeau, Kirchhoff, and Fraunhofer, Michelson, Zernike [1], along with many others who contributed to the development of modern astronomy and optics.
In the current series of articles, we want to tell in more detail about the technology of grinding, polishing and testing optical mirrors for telescopes [5][7]. Due to their lower cost, relative ease of production, and some other properties, the mirror telescopes, or the so-called telescopes reflectors, have become an ultimate tool of modern amateur and professional astronomy. Practically, all large scientific telescopes created in the last 100 years are reflectors and are still successfully working [2][8]. It would be interesting to mention that the technology for manufacturing lenses and mirrors is similar to the technology used in precious stones processing. It has remained unchanged for the last 4-6 millennia, since Ancient India and Babylon. Here we will describe the process of making concave optical surfaces for primary telescope mirrors since we have enough practical experience in this area. The fabrication of flat and convex surfaces is essentially the same.
Accuracy
Before we start with a description of the manufacturing technology, we need to consider one essential question: what accuracy do we want to achieve? In optics, there is a simple criterion for determining this accuracy called the Rayleigh criterion, named after Lord Rayleigh (John William Strutt, 3rd Baron Rayleigh) [1][3][5][8]. Without going into mathematical details, we will say that according to this criterion, if the deformation of the wavefront is no more than λ/4, where λ is the wavelength of the light, then we can consider the wavefront to be ideal. Since the wavefront deformations double during reflection, the accuracy of the optical surface must be no smaller than λ/8 or λ/10. At a typically visible light wavelength of about 0.5 microns (5*10-4 mm), the accuracy required is a few hundreds of thousandths of a millimeter (5*10-5 mm). Here it is not only a matter of surface accuracy in terms of its micro-roughness but of its exact geometric shape, which must hold for the entire optical surface. In modern professional telescopes, it can reach several meters in diameter!
Just imagine a modern professional telescope with a primary mirror several meters in diameter. On this piece of glass, we must create and control with the necessary geometrical precision, a surface layer, a few nanometers thick, an incredibly fine structure, thanks to which the operation of the optical instrument is possible! It sounds fantastic, really! How can this be possible, and how can this be achieved? Isn't it amazing? We hope to answer these questions in the next few articles.
As mentioned before, processing technology has been unchanged for millennia. In the last few centuries, people have learned to apply this technology not only to make beautiful shiny glasses or pebbles (any stone can be cut and polished and be incredibly beautiful, even ordinary gravel). They learned to use it to create complex optical instruments without which modern science is unthinkable. Moreover, even until now, in the professional production process, the final stage of surface polishing, the so-called figuring, is done by hand. As the opticians like to say, it is more mysticism than science.
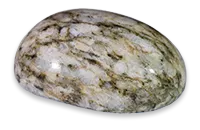
Another important aspect is related to the accuracy and difficulties in the production process, especially with an aspherical surface such as a parabola, ellipse or hyperbola. In this case, the difference δ between the surface and the tangential paraxial sphere is defined by the expression:
δ ~ εH4 / 8r3
where ε is the eccentricity, r is the paraxial radius of curvature, and H is half the mirror diameter. It is seen that δ is proportional to the first degree of the diameter and the third degree of the relative aperture A = H / r. For example, when the aperture doubles, δ increases eight times, which is an order of magnitude more [4][5]. All this means that the fabrication of large aspherical surfaces is a very complex process and requires really unique skills.
Read more about optical surface processing in the second part of our series.
Reference
- Born M., Wolf E.
Principles of optics. Electromagnetic theory of propagation, interference and diffraction of light
, Pergamon Press, 4th Edition, 1968. - Pacini et al.
Optical telescopes of the future
, ESO Conference, Geneva, 1978. - Walker G.
Astronomical observations. An optical perspective
, Cambridge University Press, 1987. - Максутов Д.
Астрономическая оптика
, Наука, 1979. - Максутов Д.
Изготовление и исследование астрономической оптики
, Наука, 1984. - Михельсон Н.
Оптические телескопы. Теория и конструкция
, Наука, 1976. - Навашин М.
Телескоп астронома-любителя
, Наука, 1979. - Попов Г.
Современная астрономическая оптика
, Наука, 1988.