Шлифоване и тестване на огледала за телескопи – част 2
Тех инфо | 12 юли 2022
Шлифоване
Основният материал за изготвяне на оптични огледала е стъклото. Евтино е, обработва се сравнително лесно, позволява изготвянето на висококачествени оптични повърхности, твърдо е и това го прави устойчиво на надраскване. Но може би най-важното му качество е неговата стабилност във времето. Запазва свойствата си в продължение на векове, без изменение. Подходящи са марки с нисък температурен коефициент на линейно разширение. Такива са кварцовите стъкла (боросиликатни стъкла) и стъклокерамиката (Ситал, Zerodur). При подбора на стъклената заготовка е важно съотношението между дебелината и диаметъра. От това зависи степента на провисване и механична деформация в етапа на производство и след това, при монтирането на огледалото в телескопа. Колкото е по-тънка заготовката, на толкова повече независими опорни точки трябва да се разтовари
[1][3].
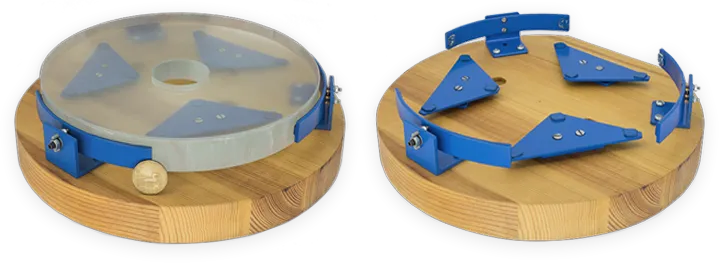
Казано най-накратко, технологията за шлифоване на стъклото представлява притриване на повърхността му с използване на абразивно-водна суспензия от твърд абразивен прах с определена едрина на зърното, смесен с вода. Шлифоването започва с етапа на издълбаване на стъкления диск, за да му се предаде грубо форма на вдлъбната сфера. Използва се абразив с едро зърно и най-често, малък метален пръстеновиден шлифовалник [3][4]. Формата на полученото издълбаване се контролира с прецизен микрометричен дълбокомер с точност от 0.01 mm и по-висока.
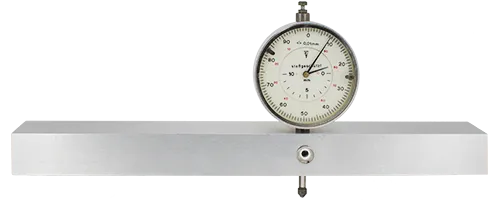
Размерът на абразивното зърно се обозначава в микрони (µm) или в мешове (mesh). Последното е извънсистемна имперска единица за измерване и води началото си от преди векове. Мешовете са броя дупки в сито с размер един квадратен инч (25.4 x 25.4 mm). Колкото дупките са по-малки, толкова числото мешове е по-голямо. За пример, едрината на шкурката и до сега е прието да се означава в мешове. В миналото, ситото е представлявало текстилна тъкан, изтъкана от нишки с определена дебелина и е служило за пресяване на брашно или други прахообразни продукти. Абразивите се произвеждат под формата на прах с определена едрина на зърното. За материал се използват твърди карбиди и окиси като корунд (Al2O3), карборунд (SiC), бор карбид (B4C), кварц (SiO2) и др.
След грубото издълбаване на стъклената заготовка под приблизителна сферична форма, се пристъпва към постепенното заглаждане на повърхността, с използването на абразиви с все по-малка едрина. На този етап шлифоването се извършва със специален шлифовалник. Той представлява плоско-изпъкнала циментова отливка с кривина на изпъкналата страна отговаряща на кривината на вдлъбнатата стъклена заготовка. След втвърдяването и изсъхването на цимента, целият шлифовалник се покрива със слой от епоксидна смола. Върху изпъкналата страна се нареждат малки квадрати от полимерен материал, като се внимава центърът на получената квадратна мрежа да не съвпадне с центъра на шлифовалника. Това се прави с цел избягване на зоналните деформации, така че получената повърхност да е ротационно симетрична и с еднаква кривина навсякъде. Дискретната квадратна мрежа има някои важни предимства. Първо, в така получената система от канавки между квадратите, абразивната суспензия циркулира свободно и шлифоването е много по-равномерно. Второ, ако между триещите се повърхности случайно попадне едра твърда частица, тя много бързо се претъркулва
в най-близката канавка и не може да надраска стъклото. Трето, с използването на по-мек полимерен материал за шлифовалника се постига много по-фин мат върху стъклото. Най-предпочитания материал за квадратите е органично стъкло (плексиглас), но може да се приложи и който и да е друг подобен полимер.
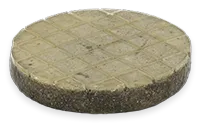
Стъклото започва да се шлифова чрез шлифовалника, на няколко етапа, като при всеки следващ етап се използва все по-фин абразив [2][3][4]. Даден етап привършва, когато микрограпавините от предходния се скрият напълно. Между отделните стадии всичко се измива много добре и качеството на повърхността се следи със силна лупа. Движенията на шлифовалника спрямо стъкления диск са плавни и овални, с взаимно завъртане на двата детайла един спрамо друг. Могат да се извършват на ръка или машинно. Първоначалното притриване започва с абразив с едрина 300 – 400 µm, като на всеки следващ етап размерът на абразива се намаля 1.5 – 2 пъти. Шлифоването се прекратява при достигане на едрина от 14 µm или дори 10 µm. По-нататъшно намаляване не е желателно, тъй като вероятността за попадане на прашинка между триещите се повърхности и получаване на дълбоки драскотини, е много голяма. Когато това се случи (не дай Боже!), шлифоването се връща на етапа на грубата шлифовка и всичко започва отначало. Ето защо, на последните стадии на фина обработка, чистотата във всичко трябва да е безупречна!
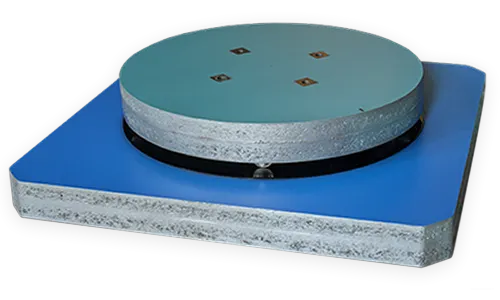
По време на шлифоването трябва да се прошлифоват страничната и задната повърхности на огледалото. Това се прави не само с декоративна цел, но и за да се премахнат повърхностните напрежения получени при изливането на стъклената заготовка.
Когато привърши процесът на фината шлифовка, се пристъпва към следващия етап от обработката – полирането на повърхността.
Четете подробно за процеса на полиране и фигуризация на огледалата в следващата част на нашата поредица. Научете повече за точността при оптичните повърхности.
Литература
- Максутов Д.
Изготовление и исследование астрономической оптики
, Наука, 1984. - Навашин М.
Телескоп астронома-любителя
, Наука, 1979. - Наумов Д.
Изготовления оптики для любительских телескопов-рефлекторов и ее контроль
, Наука, 1988. - Сикорук Л.
Телескопы для любителей астрономии
, Наука, 1982.